Линии ЛГС, 1000-1500 кг в час (опил)
15 000 000 ₽
Запросить кп
.jpg.webp)
Описание линии прессования древесных гранул
Предлагаемая технология предназначена для получения пеллет. В качестве сырья используют древесный опил естественной влажности 50-55%. Плановая производительность линии – 1000 и 1500 кг/час. Технология предусматривает сушку сырья, после которой влажность опила снижается до приемлемого уровня 12%. Полуфабрикат достаточно дисперсный – в предварительной стадии измельчения не нуждается.
В состав линии входит автоматизированный теплогенератор, который также работает на опиле. За счет этого технология становится не только высокопроизводительной, но и экономически выгодной.
Наша компания «АЛБ Групп» уже 10 лет присутствует на российском рынке переработки биомассы. Накоплен большой опыт производства оборудования для промышленного прессования гранул/пеллет, его монтажа и пусконаладочных работ. Мы предлагаем не просто оборудование и технологию.
Вместе с автоматизированной линией по выпуску пеллет вы получаете:
- полное техническое сопровождение – от разработки проекта до его запуска, т.е. полностью под ключ;;
- профессиональную техническую поддержку и сервис с использованием оригинальных запчастей;
- всем клиентам предоставляем 12 месяцев гарантии от завода-производителя с возможностью продления договора.
Наименование | ЛГС-1000 (опил) | ЛГС-1500 (опил) |
Производительность, кг в час | 800 – 1000 | 1200 – 1500 |
Установленная мощность, кВт | 201 | 256 |
Необходимая площадь помещения, м2 | 250 – 400 | 350 – 600 |
Максимальная высота, м | 6,5 | 6,7 |
Кол-во персонала, чел | 2 – 3 | 2 – 3 |
Цена, руб. | от 17 000 000 | от 21 000 000 |
*большинство значений, указанных в таблице, являются базовыми для типовых линий. При реализации проекта каждая линия согласовывается индивидуально с Заказчиком, поэтому часть показателей, как правило, отличается от базовых значений.
Технологическая линия прессования пеллет
Процесс изготовления гранул можно разделить на несколько последовательных технологических операций, каждой из которых отвечает участок комплексной линии.
Подготовительный участок
Технологическая линия начинается с бункера, куда сырье выгружается прямо из грузовика, погрузчика или трактора. Далее подача сырья на производственную линию происходит в автоматизированном режиме. Встроенные в бункер скребки сгребают опил на ленту конвейера, скорость которого можно регулировать.
Чтобы предотвратить попадание посторонних примесей в механизмы линии, в зоне выгрузки из бункера установлен специальный сепаратор. Предназначен он для распределения опила по фракциям, в том числе, отделения случайно попавших в бункер сучков, щепы и другого крупного мусора. Затем сырье проходит через бункер-распределитель, из которого автоматически подается на сушку в барабан или же в теплогенератор на сжигание.
Участок для сушки сырья
Технология производства гранул предусматривает снижение влажности сырья с 50% и более до приемлемых 12-14%. Для этого опил поступает в сушильный барабан. Для сушки применяют горячие газы из теплогенератора. Для транспорта этих топочных газов используется дымосос. В целях пожарной безопасности блок оснащен искрогасителем. На входе и выходе из сушильного барабана температура гранул соответственно составляет 300-350 оС и 80-100 оС.
В камере барабана вследствие испарения влаги под воздействием турбулентного потока горячих газов осуществляется сушка сырья. Смесь сырья и газов из камеры сушильного барабана поступает в циклон. В нем отделяется твердая фаза от газообразной – доведенный до 12-14% влажности опил осаждается и затем через шлюзовый затвор удаляется из циклона. Водяные пары под воздействием дымососа по каналам воздуховода отводятся в окружающее пространство. Для удобства обслуживания техпроцесса в линиях производительностью от 1000 кг/час система автоматизации устроена таким образом, что оператору остается только выставить конечную температуру продукта.
Участок сушки в линии производства пеллет – один из наиболее ответственных, поскольку в гранулятор должно поступать сырье влажностью более 12-14%. В зависимости от сезона и погоды этот показатель может очень существенно различаться – ниже 50% летом, 55% и выше в осенне-зимний период, что напрямую сказывается на производительности участка сушки. Зависимость эта нелинейная – количество испаренной влаги на единицу объема возрастает по экспоненциальной зависимости.
Повышенная влажность сырья создает и еще одну проблему – процесс горения значительно ухудшается, вследствие чего теплогенератору сложнее выйти на проектную мощность (а может и вообще не выйти), что еще больше усугубляет ситуацию. Чтобы такого не случилось, для сушильных комплексов мы берем значительный запас производительности. Просьба к клиентам – учитывайте это при согласовании деталей проекта или же при самостоятельном выборе оборудования. При работе с древесным материалом принимают во внимание только один критерий влажности сырья – относительную влажность.
Участок измельчения сырья
Технологическая зона измельчения состоит из пневматической дробилки (молотковой) и циклона со шлюзовым затвором. Принцип действия дробилки напоминает принцип действия пылесоса – система всасывает сухое сырье (опил), измельчает его до необходимой фракции, после чего с потоком воздуха подает на участок гранулирования. После прохождения циклона и шлюзового затвора уже измельченное сырье осаждается в бункере над гранулятором. Это позволяет существенно снизить уровень выброса пыли в зоне работы автоматической линии.
Участок гранулирования
Подготовленное сухое сырье поступает на участок гранулирования, который состоит из 2 частей – бункера-ворошителя и пресс-гранулятора. В бункере-ворошителе создается оперативный запас сырья. Фактически, агрегат выполняет функцию демпфера – он обеспечивает согласованную работу молотковой дробилки и пресс-гранулятора. Наличие ворошителя в устройстве бункера предупреждает слеживание продукта. Специальная конструкция бункера и правильный подбор мощности привода обеспечивает эффективную защиту мотор-редуктора от перегрузки.
Другими словами, предотвращает выход из строя и простои всей линии, как это порой случается при использовании некачественных аналогов. В линии производства пеллет нет места «слабому звену», остановка которого парализует все производство. Вот почему компания ALB Group так тщательно подходит к разработке каждого элемента.
Пресс-гранулятор – узел, отвечающий непосредственно за производство пеллет. Гранулы формируются под высоким давлением – в конструкции гранулятора имеются специальные вальцы, которые и продавливают подготовленное сырье сквозь отверстия матрицы. Компания ALB Group производит 2 группы грануляторов – собственная линейка (ALB) и ОГМ-1,5 на базе разработок советского времени. Комплектующие для грануляторов – собственного производства или от проверенного поставщика. Литье и шестерни – отечественного производства, матрицы и отдельные детали импортного производства заказываем у немецкой компании, имеющей представительство в РФ. Таким образом, и в 2022 году поставки бесперебойны.
Такой подход к ведению бизнеса полностью оправдал себя – наши грануляторы одни из самых надежных на российском рынке. Особенность линейки грануляторов АЛБ – комплекс доработок, обусловленных спецификой производства именно топливных пеллет. По сравнению с комбикормами древесный опил гранулируется значительно труднее, но эта техническая проблема была успешно решена за счет усовершенствования подготовительного участка.
Участок охлаждения пеллет и фасовки готового продукта
После прессования пеллеты имеют избыточную температуру (примерно 80 оС) и влажность. Чтобы охладить гранулы и удалить из них лишнюю влагу, в колонне охлаждения пеллеты продувают воздухом из окружающей среды – такая несложная операция позволяет стабилизировать состав гранул, сделать их более прочными. На участок охлаждения готовые гранулы подаются при помощи ленточно-скребкового конвейера.
Готовые охлажденные гранулы фасуют в биг-бэги и/или в удобные для реализации мешки от 5 до 50 кг. Для отмеривания продукта линия производства пеллет от «АЛБ Групп» комплектуется полуавтоматическим весовым дозатором. Если вам понадобится индивидуальное предложение по комплектации оборудования, наши менеджеры выслушают вас и подготовят индивидуальный проект, учитывающий особенности вашего бизнеса.
Основные узлы линии гранулирования пеллет
Теплогенератор. Основное его назначение – производство сушильного агента. Сжиганием опила (щепы) в камере генератора получают топочные газы, которые в смеси с воздухом и применяют для сушки сырья. Оборудование работает в автоматическом режиме.
Тепловая мощность теплогенератора – от 1,0 до 2,5 МВт
Сушильный барабан. Устройство для непосредственной сушки сырья – в нем доводят относительную влажность материала до необходимых для гранулирования 14%. В сушильной камере под воздействием сушильного агента сырье постепенно теряет избыточную влажность. Чтобы сырье не слеживалось и равномерно отдавало влагу, барабан вращается на специальных роликах. Для этой же цели в конструкции барабана предусмотрены особые лопатки, отбойные плиты в один или несколько (в зависимости от модели) контуров.
Производительность сушильного барабана – от 500 до 2500 кг/час.
Дробилка. Устройство понадобится для измельчения подаваемого сырья – в том числе, и крупной щепы, и других фракций до нужного для прессования размера частиц. Дробилка укомплектована сепаратором с неодимовым магнитом – такое устройство хорошо справляется с очисткой сырья от металлических включений. Чтобы предотвратить/погасить вибрацию, агрегат оснащен амортизирующими крепежными опорами. Для измельчения крупной фракции древесных отходов (щепы, горбыля) данная серия не подходит – требуется оборудование иного типа.
Производительность дробилки – от 700 до 1500 кг/час.
Мощность дробилки – от 18,5 до 30 кВт.
Пресс-гранулятор. Основной узел, «сердце» технологии изготовления пеллет. Именно в нем и формируются гранулы заданной геометрии и свойств. В зависимости от нужной производительности линии используют клиноременной гранулятор ALB или редукторный ОГМ-1,5М серии. Все ответственные детали грануляторов (крышки прессующего узла, дозатор, смеситель) изготовлены из высококачественной хромистой нержавейки, что значительно увеличивает их эксплуатационный ресурс.
Производительность – от 500 до 2000 кг/час.
Мощность – от 55 до 150 кВт.
Колонна или блок охлаждения. Данный узел необходим для охлаждения уже готовых гранул, а также их сортировки. Готовый продукт (пеллеты) поступают на стол рассева, где и обеспечивается отделение несгранулированных частиц от готового продукта. Бывают ручного типа разгрузки или автоматического. Блок охлаждения, в отличие от колонны охлаждения, имеет циклон и шлюзовый затвор – эти устройства обеспечивают дополнительную аспирацию и понижают концентрацию взвешенной в воздухе пыли.
Производительность узлов охлаждения – от 500 до 3000 кг/час.
Мощность – от 3,5 до 26,5 кВт.
Оборудование в составе
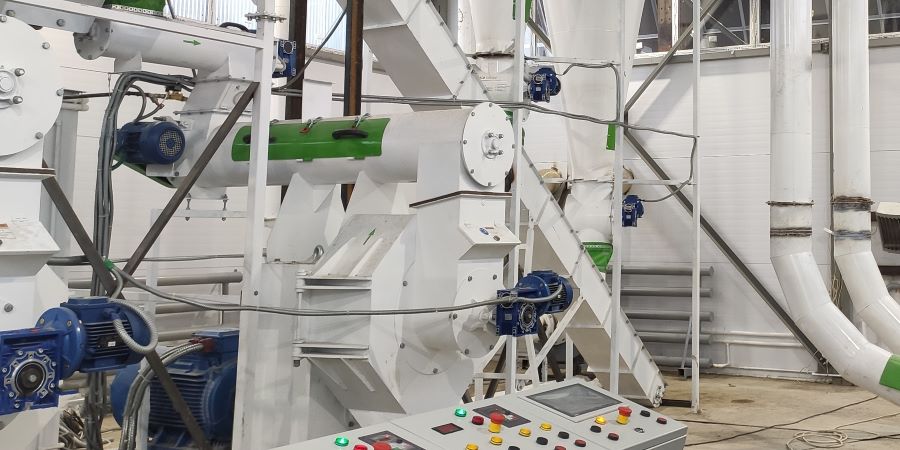
Пресс-грануляторы серии ОГМ
Пресс-грануляторы серии ALB
Сушильные барабаны АВМ
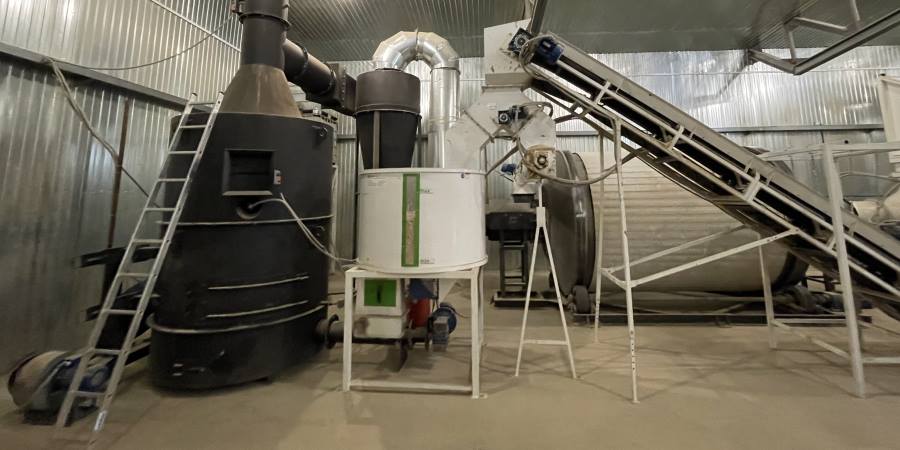
Теплогенераторы ТГ
Ленточные скребковые конвейеры КЛС
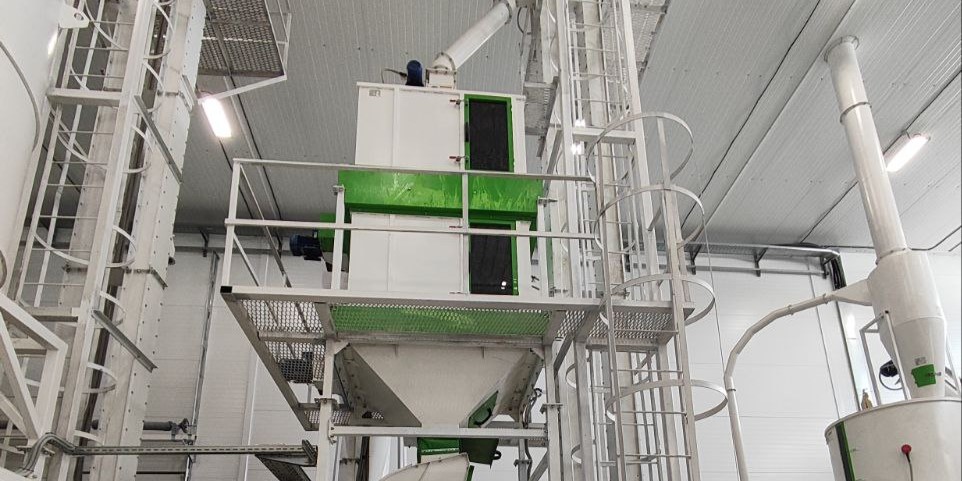
Блоки охлаждения АБО
Дробилки молотковые ДМ
Сепаратор дисковый
Весовой дозатор
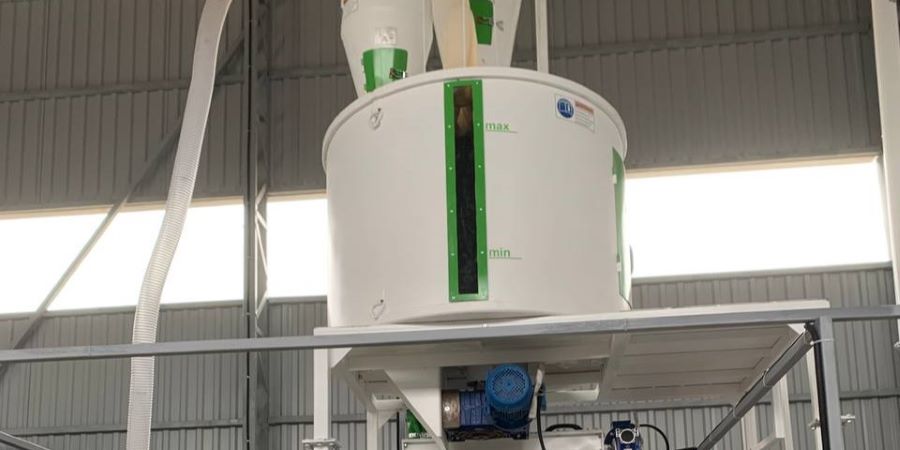
Бункеры-ворошители БВ