Линии ЛГС, 2000-2500 кг в час (щепа, опил, горбыль, баланс)
30 000 000 ₽
Запросить кп
.jpg.webp)
В данном разделе представлены пеллетные линии с высокой автоматизацией, способные перерабатывать различное древесное сырье с относительной влажностью 50-55%. Производительность 2000 и 2500 кг/ч. Особенностью данных технологий является значительный уровень технологичности и автоматизации, необходимость которых обусловлена высокой производительностью.
Почти 10 лет опыта производства оборудования для изготовления пеллет, осуществления монтажей и пуско-наладок делают компанию ALB Group экспертом в области переработки биомассы, одной из лидирующих компаний на российском рынке. Мы смело заявляем - мы полностью берем на себя весь технологический процесс!
Выбирая сотрудничество с ALB Group вы получаете:
- комплексную производственную линию под ключ: мы позаботимся обо всем от подбора нужной вам технологии до монтажа готовой линии;
- долгосрочные прозрачные отношения: качественное сервисное обслуживание, постоянное наличие запасных частей, техническую поддержку;
- заводскую гарантию 12 месяцев с возможностью продления.
Наименование | ЛГС-2000 | ЛГС-2500 |
Производительность, кг в час | 1600 – 2000 | 2000 – 2500 |
Установленная мощность, кВт | 535 | 645 |
Необходимая площадь помещения, м2 | 900 – 1200 | 900 – 1200 |
Максимальная высота, м | 8 | 8 |
Кол-во персонала, чел | 2 – 3 | 2 – 3 |
Цена, руб. | от 40 000 000 | от 45 000 000 |
*большинство значений, указанных в таблице, являются базовыми для типовых линий. При реализации проекта каждая линия согласовывается индивидуально с Заказчиком, поэтому часть показателей, как правило, отличается от базовых значений.
Процесс производства можно условно разбить на участки:
Участок предварительного измельчения и подачи сырья
На первом этапе линии установлена рубительная машина для измельчения кусковых отходов (горбыль, баланс и т.д.). Ее мощность зависит от габаритов измельчаемого сырья и необходимой производительности. На выходе из рубительной машины получается щепа, которая по конвейеру подается на склад с подвижным полом. Привозная щепа также может подаваться сюда же напрямую. Данный склад, в отличии от приемных механизированных бункеров, выполняет роль не только автоматизированной подачи, но и обеспечивает функцию хранения – его объем составляет 75 – 150 м3.
На выгрузке со склада установлен сепаратор, предназначенный для отделения посторонних примесей. Часть щепы уходит на обслуживание теплогенератора, а основная часть – поступает в молотковую дробилку для предварительного измельчения перед сушкой.
Участок сушки
Предназначен для снижения влажности с 50-55% до 14%. Сушка опила происходит в сушильном барабане за счет горячего воздуха (агент сушки), который попадает туда из теплогенератора с помощью дымососа. Агент сушки представляет из себя смесь воздуха и топочных газов, образующихся при сжигании. Топочный блок оборудован искрогасителем, предотвращающим попадание искр в сушильный барабан. Температура на входе в барабан до 400оС (обычно 300 – 350); на выходе – 80 – 100оС.
В результате в барабане, в потоке движущейся смеси горячего воздуха и сырья, происходит испарение влаги. Смесь сырья и пара из барабана попадает в циклон, входящий в состав пневмотранспорта. Там происходит отделение высушенного опила от пара: сырье осаждается и покидает циклон через шлюзовой затвор, а пар продолжает движение по воздуховодам пневмотранспорта и проходя через дымосос выбрасывается в окружающую среду.
Для линий от 1000 кг/ч применяются теплогенераторы, работающие на опиле или щепе в автоматическом режиме - оператору необходимо только задать температуру, которую необходимо обеспечить на выходе.
Сушка сырья – один из самых ответственных участков пеллетной линии. Зачастую этому процессу не уделяют должного внимания, т.к. принято считать, что в линии гранулирования самое важное – гранулятор. Важность качества и надежности сушильного комплекса обусловлена тем, что исходная влажность сырья может существенно варьироваться – летом она может быть ниже 50% и сушка будет работать отлично, но в остальное время сырье может переувлажняться и быть существенно выше 55%. Причем зависимость производительности от относительной влажности не линейная, а идет по экспоненте. Т.е. если влажность 65%, а не 55%, то нужно испарить в 1,5 раза больше воды из сырья.
Кроме того, у переувлажненного сырья ухудшается процесс горения; теплогенератор может просто не выходить на проектные мощности, и ситуация с сушкой еще более усугубляется. Поэтому мы берем существенный запас по производительности для своих сушильных комплексов, и просим наших клиентов учитывать эти моменты при согласовании проекта, а также акцентировать на этом внимание при выборе оборудования, т.к. некоторые аналоги по паспорту достигают своей производительности при съеме влаги с 35% (фактически полусухое сырье, в природе редко встречающееся), а где-то ссылаются на абсолютную влажность, которая считается по другой формуле. При работе с древесиной всегда используется относительная влажность.
Оперативный склад сухого сырья и участок измельчения
На линиях высокой производительности после сушильного комплекса рекомендуется устанавливать склад оперативного хранения сухого сырья. Такое количество оперативных складов сырья на разных участках обусловлено необходимостью снизить зависимость участков друг от друга, чтобы в случае обслуживания или остановки одного из участка, остальная линия могла продолжать стабильную работу продолжительное время. На данном участке может быть установлен как механизированный бункер (объем до 40 м3), так и стокерный пол (объем 75 – 150 м3).
Для финального измельчения сырья перед гранулированием в данной технологии используются молотковые дробилки серии ДМ, обладающие большей надежностью и ресурсом в сравнении с пневматическими дробилками.
Участок гранулирования
Состоит из бункера-ворошителя и пресс-гранулятора.
Бункер-ворошитель выполняет роль оперативного склада сырья (демпфера). Он необходим для согласования работы молотковой дробилки и пресс-гранулятора. Бункер оборудован ворошителем для того, чтобы опил не слеживался и не «зависал». Конструкция бункера и мощность привода подобраны оптимальным образом, чтобы избежать как слеживания продукта, так и перегрузки мотор-редуктора. Это, в свою очередь, предотвращает нежелательные остановки и простои всей линии, что бывает при использовании некачественных аналогов. Любая пеллетная линия представляет из себя цепочку, и остановка какого-либо элемента вызывает остановку всего производства, поэтому для ALB Group нет мелочей в линии, важен каждый ее элемент.
Непосредственное формирование пеллет происходит в пресс-грануляторе – гранулы образуются при прохождении подготовленного сырья через отверстия матрицы, куда они продавливаются с помощью пресс-вальцов. Имеются две серии производимых ALB Group грануляторов – собственная линейка ALB, а также линейка на базе советского ОГМ-1,5. Часть комплектующих (литье, шестерни) – заказываются на российских заводах, матрица – немецких производств (GRAF или Münch) или итальянского производства (General Dies), подшипники и РТИ – производства ЕС, все остальное – собственного производства.
Данные особенности делают наши грануляторы более надежными в сравнении с аналогами, представленными на российском рынке. Кроме того, гранулятор имеет некоторые доработки, обусловленные спецификой̆ гранулирования топливных пеллет (трудногранулируемое сырье в сравнении с комбикормом). Эти доработки позволяют более эффективно подготавливать сырье в смесителе-кондиционере, обеспечивают удобство обслуживания всех рабочих элементов, эффективно удаляют пар из прессующего узла и т.д. – все эти нюансы в итоге влияют на производительность и качество конечного продукта.
Участок охлаждения и фасовки
Колонна охлаждения необходима для охлаждения пеллет после прессования. Гранулы после формирования имеют температуру порядка 80оС, а также избыточную влажность. В колонне происходит продувание гранул воздухом из окружающей среды, в итоге они остывают до температуры приближенной к температуре окружающей среды, а также удаляется избыточная влажность. Если этого не сделать, гранулы начнут преть и рассыпаться.
Подача гранул на участок охлаждения осуществляется с помощью ленточно-скребкового конвейера. Фасовка осуществляется в биг-бэги и/или в мешки от 5 до 50 кг, для чего устанавливается полуавтоматический весовой дозатор.
Наши опытные менеджеры знают все нюансы технологий и с радостью подготовят профессиональное индивидуальное предложение, решающее именно ваши задачи!
Теплогенератор
Предназначен для производства сушильного агента (смеси воздуха и топочных газов), благодаря которому в дальнейшем происходит сушка сырья. Теплогенераторы ТГ работают в автоматическом режиме; сырьем служат древесные опил и щепа.
Тепловая мощность: 1 – 2,5 МВт
Сушильный барабан
Здесь происходит непосредственная сушка сырья. Поток горячего воздуха, двигаясь через сушильный барабан, постепенно перемещает сырье, в процессе чего происходит испарение избыточной влаги. Барабан вращается на роликах, а также его конструкция имеет специальные лопатки, отбойные плиты и (у некоторых моделей) – несколько контуров. Все эти конструктивные особенности необходимы для качественной равномерной сушки сырья.
Производительность: 500 – 2500 кг в час
Дробилка серии ДМ
Предназначена для предварительного измельчения щепы до фракции, подходящей для эффективной сушки, а также после сушильного комплекса для финального измельчения сырья перед гранулированием. Работают только в комплекте с пневмотранспортом, обеспечивающим разгрузку дробилки.
Производительность: 700 – 2500 кг/ч
Мощность: 22 – 75 кВт
Пресс-гранулятор
Ключевой и наиболее дорогостоящий узел данной технологии, в котором происходит непосредственное формирование гранул. Применяются грануляторы серий ALB и ОГМ-1,5М – в зависимости от требуемой производительности. Серия ALB – клиноременный, ОГМ – редукторный. Крышка прессующего узла, смеситель и дозатор выполнены из нержавеющей стали, что значительно продлевает их срок службы.
Производительность: 500 – 2000 кг/ч
Мощность: 55 – 150 кВт
Колонна или блок охлаждения
Необходимы для охлаждения готовых гранул. Включают в себя стол рассева, обеспечивающий отделение несгранулированной части от готового продукта. В зависимости от уровня автоматизации бывают с ручной и автоматической разгрузкой. Блок охлаждения отличается от колонны наличием дополнительной аспирации (циклон и шлюзовой затвор), снижающий уровень пыли.
Производительность: 500 – 3000 кг/ч
Мощность: 13,5 – 26,5 кВт
Оборудование в составе
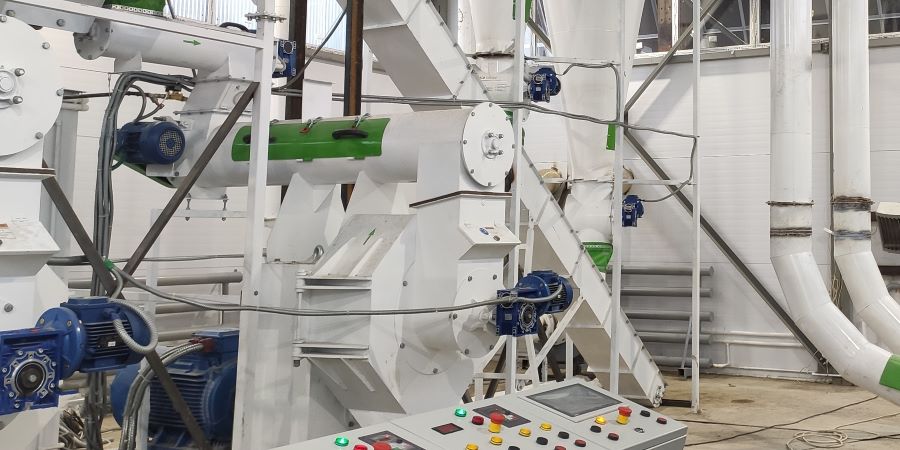
Пресс-грануляторы серии ОГМ
Пресс-грануляторы серии ALB
Сушильные барабаны АВМ
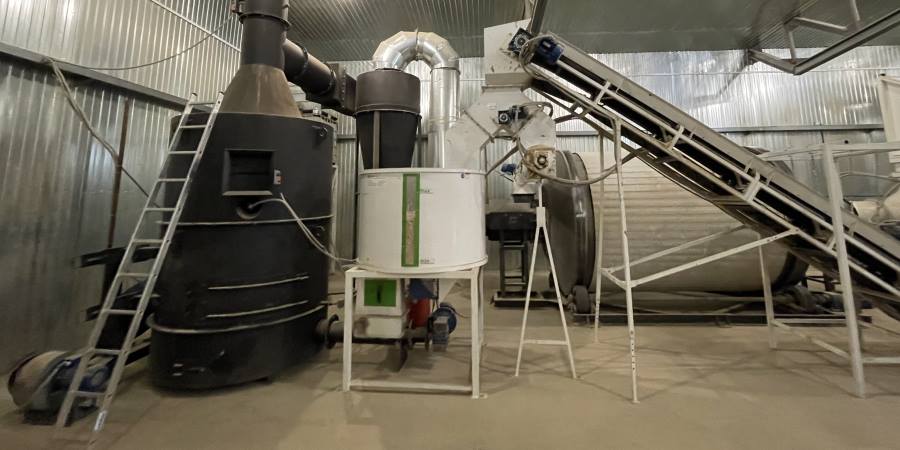
Теплогенераторы ТГ
Ленточные скребковые конвейеры КЛС
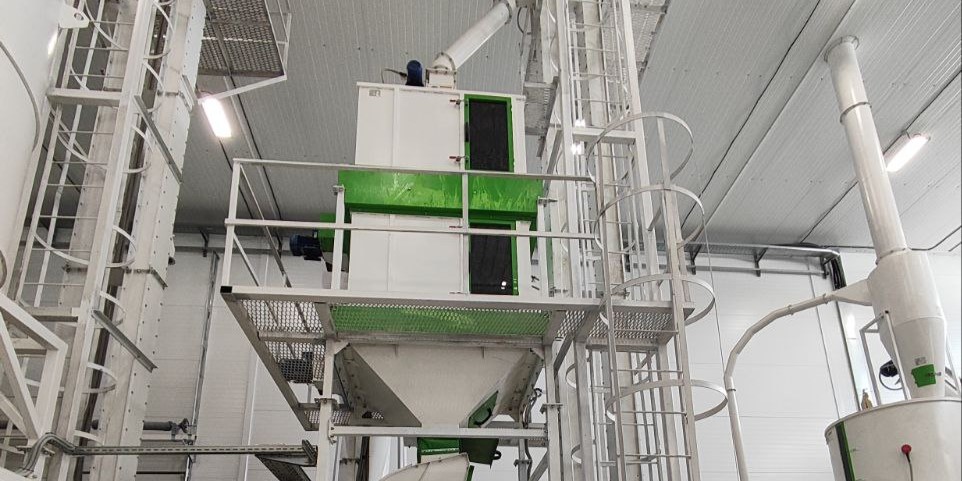
Блоки охлаждения АБО
Дробилки молотковые ДМ
Рубительные машины БРМ
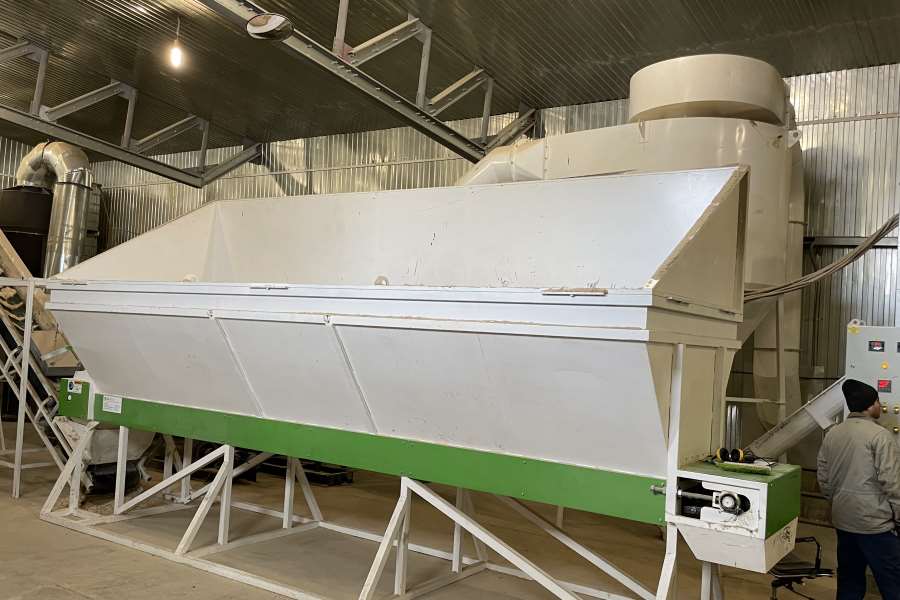
Бункеры механизированные БМ
Стокерный пол СП
Сепаратор дисковый
Весовой дозатор
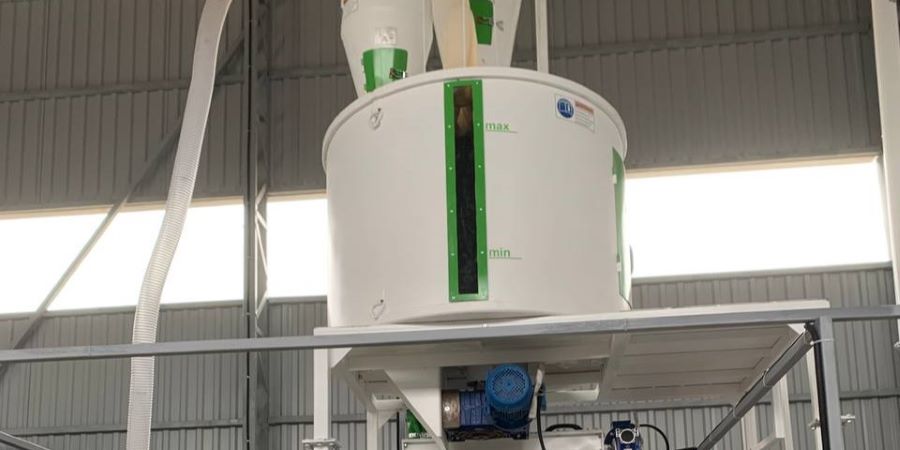
Бункеры-ворошители БВ