Линии ЛГС с ТТБ, 500-1000 кг в час (опил, щепа)
8 500 000 ₽
Запросить кп
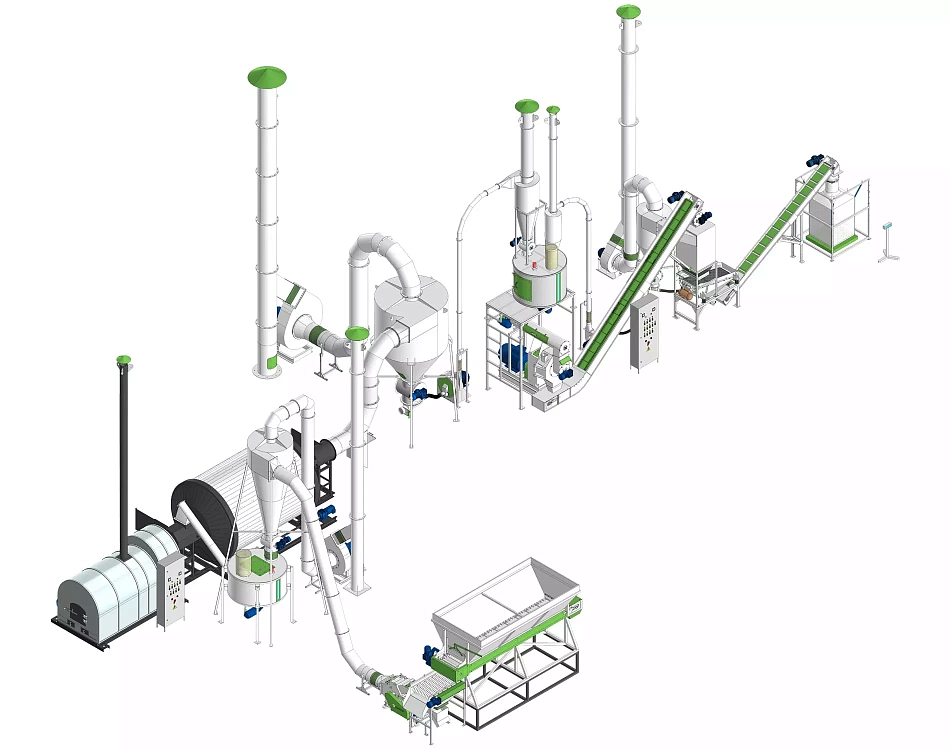
Описание ЛГС
Для производства топливных гранул компания ALB Group изготавливает линии гранулирования древесины серии ЛГС с ТТБ. Их производительность в час составляет от 300-500 кг до 800-1000 кг.
Природная влажность сырья – около 55% (в пересчете на относительные единицы), для процесса гранулирования ее необходимо снизить до оптимального уровня 12%. Эта задача решается включением сушильного комплекса. Его особенность заключается в использовании топочного блока ТТБ, который работает на сжигании кусковых отходов деревообработки.
Такой вариант комплектации ЛГС – оптимальное конструктивное решение для линий с невысокой производительностью (в час менее 700 кг) и допускается к установке на ЛГС с производительностью в час от 700 до 1000 кг. При более высоких показателях линии комплектуются автоматическими теплогенераторами, которые работают на мелких древесных отходах.
Компания ALB Group за 10 лет работы на отечественном рынке промышленного производства пеллет приобрела бесценный практический опыт по внедрению технологии. Мы знакомы со всеми особенностями процесса.
Преимущества сотрудничества с компанией ALB Group:
- полное комплексное сопровождение проекта под ключ – от выбора подходящей вашим задачам технологии до монтажа и запуска ЛГС;;
- оперативная техническая поддержка и качественное сервисное обслуживание ЛГС, что обеспечивается постоянным наличием запчастей и высокой квалификацией наших специалистов;
- 12 месяцев гарантии от завода-изготовителя с возможностью заключения договора о продлении гарантийных обязательств.
Наименование, сырье | ЛГС-500 (опил) | ЛГ-700 (опил) | ЛГ-700 (щепа) | ЛГ-1000 (опил) | ЛГ-1000 (щепа) |
Производительность, кг в час | 350 – 500 | 550 – 700 | 550 – 700 | 800 – 1000 | 800 – 1000 |
Установленная мощность, кВт | 128 | 149 | 199 | 182 | 245 |
Необходимая площадь помещения, м2 | 170 – 260 | 170 – 260 | 180 – 270 | 170 – 260 | 180 – 270 |
Максимальная высота, м | 6,2 | 6,5 | 6,5 | 6,5 | 6,5 |
Кол-во персонала, чел | 2 – 3 | 2 – 3 | 2 – 3 | 2 – 3 | 2 – 3 |
Цена, руб. | от 8 800 000 | от 9 500 000 | от 10 500 000 | от 10 500 000 | от 11 500 000 |
*большинство значений, указанных в таблице, являются базовыми для типовых линий; при реализации проекта каждая линия согласовывается индивидуально с Заказчиком, поэтому часть показателей как правило отличается от базовых значений.
Технологический процесс производства пеллет
Специальная технология позволяет получать топливные гранулы из древесного сырья различных отходов деревообработки. Непосредственно для производства пеллет используются более мелкие (опил и щепа), а крупные кусковые (горбыль и другие отходы) подаются для сжигания в топочный блок.
Всю линию условно можно разделить на отдельные звенья технологической цепочки. Остановимся чуть подробнее на каждом.
Подготовка и подача сырья
Сырье на линию пеллетирования поступает через механизированный бункер. Удобство конструкции заключается в возможности загружать сырье буквально «с колес» – прямо из самосвала или погрузчика. Из приемного бункера при помощи пары металлических скребков сырье подается на ленту транспортера. Скорость подачи регулируется на панели управления. При необходимости (для экономии) данный участок можно не включать в технологическую цепочку – можно производить загрузку сырья на конвейер вручную.
Приемный бункер в зоне выгрузки (еще до попадания сырья на ленту транспортера) оснащен сепаратором. Он не допускает попадания посторонних примесей на линию. При использовании щепы в качестве сырья (более крупной по сравнению с опилом фракции) в схему ЛГС дополнительно включают дробилку молоткового типа.
ДМ позволяет дробить щепу до размера частиц, при которых процесс сушки происходит наиболее качественно. Молотковая дробилка всегда комплектуется пневмовыгрузкой – иначе устройство не сможет функционировать, так как забивается сырой измельченной древесиной.
Сушка
Участок сушки состоит из сушильного барабана в комплекте с топочным блоком. Непосредственно в сушильном барабане производится испарение влаги из измельченной древесины за счет продувки горячим воздухом в смеси с топочными газами – так называемым агентом сушки. Топочные газы образуются при сжигании кусковой древесины и крупнокусковых отходов. Из соображений пожаробезопасности ТТБ оснащен искрогасителем. Подача агента сушки в камеру сушильного барабана осуществляется посредством дымососа. При продувании через камеру температура агента сушки меняется от примерно от 400 оС на входе до примерно 100 оС на выходе.
Древесное сырье в камере барабана фактически находится во взвешенном состоянии. Затем из барабана эта воздушная взвесь измельченной древесины попадает в циклон. При выходе из него под воздействием центростремительных сил просушенный опил отделяется от парообразной фазы – измельченная древесина под действием гравитации осаждается и затем уходит из циклона через шлюзовый затвор, а горячий влажный пар удаляется в окружающее пространство при помощи дымососа.
Для относительно недорогих линий с ручной загрузкой и производительностью до 700 кг в час целесообразно применять ТТБ, работающие на крупнокусковых отходах древесины. Они дешевле теплогенераторов, которые устанавливают на мощных автоматизированных ЛГС с производительностью от 1000 кг в час. От работы участка сушки сырья зависит работа всей ЛГС – и общая производительность, и непосредственно качество гранулированного продукта.
В течение сезона на переработку сырье поступает различной относительной влажности – до 50% летом (испарение воды происходит быстро) и не менее 55% в осенне-зимний период, что обуславливает более длительную сушку. Ко всему в непогоду и в осенне-весенний сезон сырье обычно переувлажнено, что дополнительно усложняет переработку – топочному блоку сложно выйти на заданную мощность.
Зная о такой особенности сушильных комплексов, мы всегда закладываем в проект запас мощности, что очень важно при использовании для гранулирования сырья различной влажности.
Измельчение
В технологической цепочке пеллетирования участок измельчения представляет собой подключенные последовательно молотковую дробилку на входе и циклон со шлюзовым затвором на выходе. Подсушенное сырье поступает в дробилку, где измельчается, и затем потоком воздуха передается уже на участок гранулирования.
Чтобы сырье осаждалось прямо в бункер гранулятора, эта взвесь измельченной биомассы и воздуха проходит последовательно через циклон и шлюзовый затвор. Этим достигается существенное снижение пылеобразования при подаче в бункер-ворошитель, расположенный на следующем участке ЛГС.
Гранулирование
Участок состоит из двух устройств – бункера-ворошителя и пресс-гранулятора, это неразрывное звено технологической цепочки.
Бункер-ворошитель фактически представляет собой накопитель сырья. Предназначен для обеспечения бесперебойной согласованной работы ДМ и непосредственно пресс-гранулятора. Конструкция бункера дополнена ворошителем. Его мощность рассчитана таким образом, чтобы предупредить возможность слеживания измельченного сырья, а также избежать перегрузки мотор-редуктора. Таким образом, исключается риск остановки работы ЛГС и всего производства – пеллетные линии от ALB Group застрахованы от такой ситуации.
Пресс-гранулятор – устройство для формирования пеллет. Измельченное сырье под воздействием вальцев продавливается через фильеры матрицы. ALB Group предлагает две линейки грануляторов – серия АЛБ и серия на основе ОГМ-1,5. Матрица сделана в Германии или Италии (GRAF, Münch или General Dies), комплектующие из ЕС, литье и шестерни изготовлены на заводах Российской Федерации, все остальные элементы конструкции – собственного производства ALB Group.
Благодаря такой комплектации, грануляторы являются надежными в эксплуатации, что очень ценится на рынке. Также устройства имеют конструктивные доработки, учитывающие специфику производства именно топливных пеллет, что значительно влияет на производительность ЛГС и качество производимого продукта.
Охлаждение и фасовка
После прессования пеллеты поступают в зону охлаждения, так как, покидая пресс-гранулятор, они имеют избыточную влажность и температуру около 80 оС. Гранулы поступают в колонну охлаждения, где производится обдув пеллет воздухом, забранным из окружающего пространства (например, цеха), – в результате чего испаряется излишняя влага, а пеллеты охлаждаются до температуры окружающей среды. Если этап принудительного охлаждения пропустить, конечный продукт начнет рассыпаться в муку.
На участок охлаждения пеллеты подаются с использованием ленточно-скребкового транспортера. После охлаждения пеллеты поступают в полуавтоматический весовой дозатор, где их фасуют в большие «биг-бэги» или мешки меньшей емкости (5-50 кг).
Основные узлы линии ЛГС
ТТБ (твердотопливный топочный блок) используется для получения топочных газов, которые в смеси с воздухом образуют сушильный агент. В ТТБ для сжигания используются крупнокусковые отходы деревообработки 1,1-1,3 м длиной.
Загрузка ТТБ преимущественно ручная (неавтоматизированная).
Тепловая мощность блока ТТБ – 0,5-1,0 МВт.
Сушильный барабан представляет собой устройство для окончательной сушки древесного сырья перед подачей его на линию пеллетирования. Опираясь на ролики, барабан совершает вращение в горизонтальной плоскости, что приводит в движение и его содержимое (опил, стружку), которое под воздействием сушильного агента интенсивно теряет влагу.
Для качественной и равномерной сушки барабан оснащен лопатками и отбойными плитами (в один или несколько контуров). Производительность сушильного барабана в час составляет 500-2500 кг.
Дробилка ДМ используется для комплектации пеллетных линий, где в пеллеты перерабатывают щепу. Оборудование производит предварительное дробление щепы до оптимальной для процесса сушки фракции. Перед гранулированием сырью требуется еще один цикл измельчения.
Производительность дробилки серии ДМ в час составляет 700-2000 кг.
Мощность агрегата – 22-60 кВт.
Дробилка серии ДРП предназначена для завершающей стадии измельчения сырья, предшествующей непосредственно процессу гранулирования. Дробилка оснащена сепаратором с неодимовым магнитом для предотвращения попадания в гранулятор не только крупного древесного мусора, но и металлических включений.
Производительность дробилки серии ДРП в час составляет 700-1500 кг.
Мощность агрегата – 18,5-30 кВт.
Пресс-гранулятор представляет собой ключевой элемент линии пеллетирования – именно в грануляторе измельченное сырье формируется в топливные гранулы. Выбор гранулятора серий ALB (клиноременной) или ОГМ-1,5М (редукторный) зависит от необходимой производительности. Самые важные детали гранулятора изготовлены из нержавейки, что значительно повышает надежность узла и продлевает его срок эксплуатации.
Производительность гранулятора в час составляет 500-2000 кг.
Мощность – 55-150 кВт.
Колонна или блок охлаждения используются для окончательного охлаждения готовых пеллет. Участок укомплектован также столом рассева для сортировки/отделения несгранулированного продукта – бывает с ручной и автоматической разгрузкой. Блок охлаждения имеет систему пылеулавливания – устанавливается циклон с шлюзовым затвором.
Производительность – количество охлажденных гранул в час составляет 500-3000 кг.
Мощность – 13,5-26,5 кВт.
Оборудование в составе
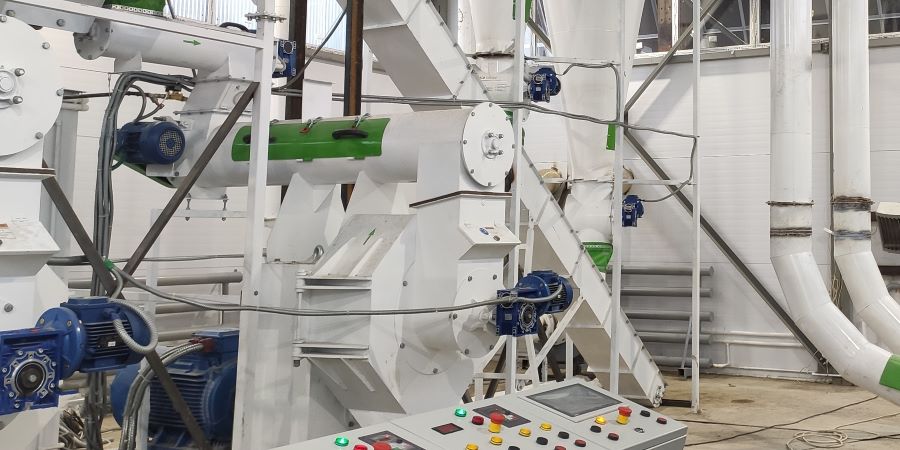
Пресс-грануляторы серии ОГМ
Пресс-грануляторы серии ALB
Сушильные барабаны АВМ
Твердотопливные топочные блоки ТТБ
Ленточные скребковые конвейеры КЛС
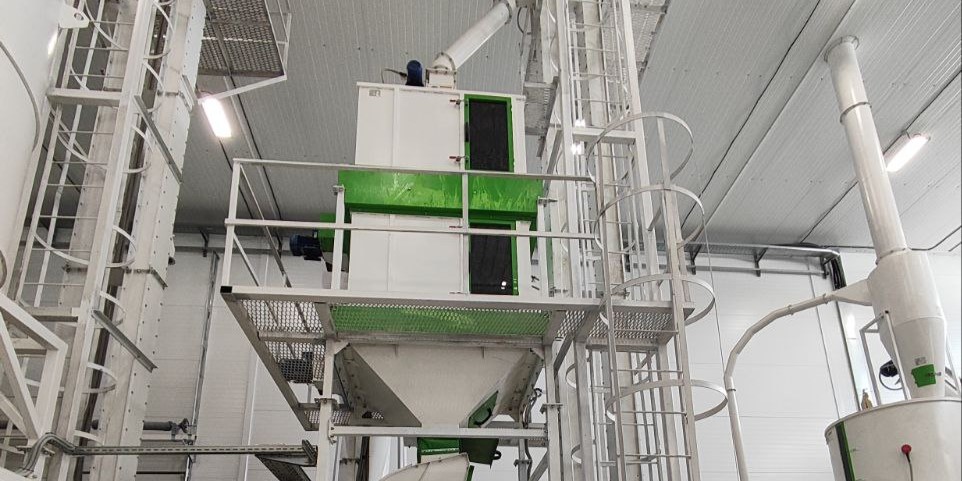
Блоки охлаждения АБО
Дробилки молотковые ДМ
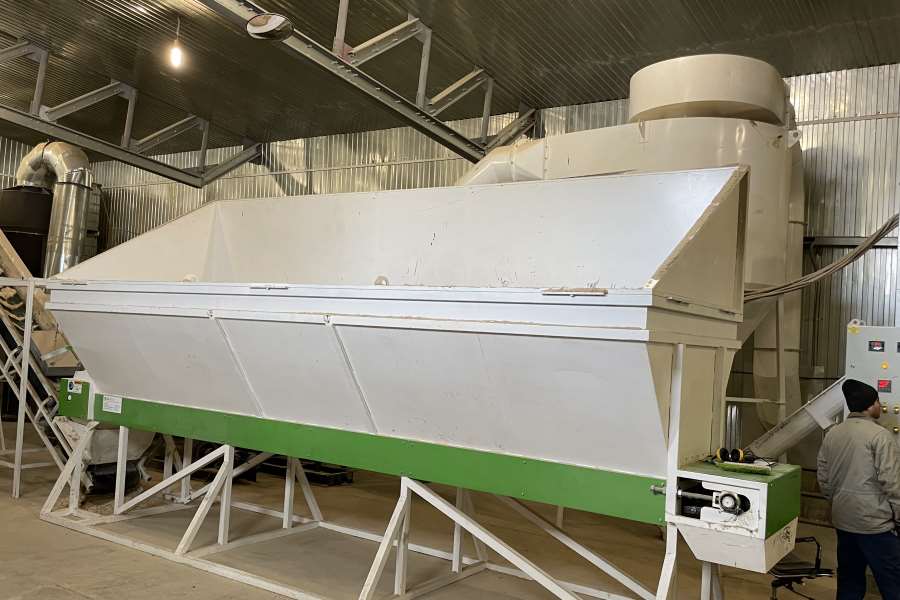
Бункеры механизированные БМ
Сепаратор дисковый
Весовой дозатор
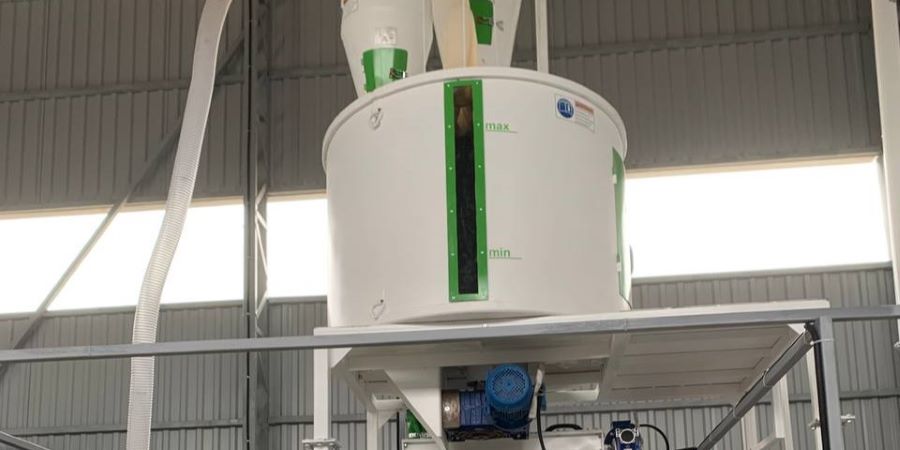
Бункеры-ворошители БВ